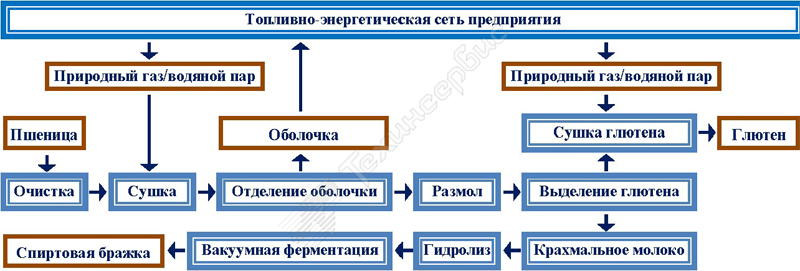
О.Г. Галузинский, начальник отдела биотехнологий ПГ «Техинсервис»
В.П. Мельничук, инженер-технолог отдела биотехнологий ПГ «Техинсервис»
_______________
Издавна человечеству известно об этиловом спирте прежде всего как об основном компоненте спиртных напитков. Кроме пищевых продуктов этиловый спирт широко используется как топливо, применяется для производства высококачественных бензинов и их высокооктановых компонентов (этил-трет-бутиловый эфир). Также этиловый спирт служит сырьём для получения многих химических продуктов (ацетальдегид, диэтиловый эфир, уксусная кислота, хлороформ, этилацетат, этилен и др.), широко применяется как растворитель (в лакокрасочной промышленности, в производстве товаров бытовой химии и многих других областях), является компонентом антифризов и стеклоомывателей, широко используется в медицине, косметологии и парфюмерии.
В связи с индустриализацией и поиском альтернативных видов топлива неуклонно растёт интерес к этанолу как к топливу.
Только за последние пять лет мировые объёмы производства топливного этанола выросли более чем в полтора раза и в 2012 году составили 106 миллионов кубических метров.
Основываясь на этом, компания «Техинсервис» 5 лет назад при определении дальнейших направлений развития обратила внимание на рынок технологий производства этанолосодержащих продуктов. Для реализации проектов этого направления на базе инженерной группы компании был создан отдел биотехнологий.
Одним из основных подходов компании «Техинсервис» при реализации инженерных идей был и остается комплексный подход к реализации проекта — от анализа и выбора технологии до успешного её внедрения.
Выбор сырья
Состав комплекса по производству этанолосодержащих продуктов в первую очередь зависит от вида перерабатываемого сырья и от способа первичной его переработки.
Компания «Техинсервис» предлагает комплексные решения по переработке как сахаросодержащего (сахарная свекла, сахарный тростник, сладкое сорго, свекловичная меласса и т.д.), так и крахмалосодержащего (пшеница, кукуруза, рожь, ячмень и т.д.) видов сырья.
Критерии выбора сырья остаются неизменными:
— стоимость;
— урожайность;
— выход целевого продукта;
— требования к переработке;
— круглогодичная доступность;
— требования к выращиванию, уборке, транспортировке и хранению;
— возможность переработки отходов (получения дополнительной прибыли).
Комплексный подход к вопросу первичной переработки сырья
Комплексный подход компании «Техинсервис» к вопросу первичной переработки крахмалосодержащего сырья (пшеницы) можно продемонстрировать на примере разработанного нашей компанией базового проекта комплекса глубокой переработки пшеницы в топливный этанол и ЭТБЭ (блок-схема технологического процесса представлена на рис. 1).
Рис. 1. Блок-схема технологического процесса первичной переработки пшеницы
Из технологических приёмов, применённых компанией «Техинсервис» в этом проекте, стоит отметить:
- Отделение оболочки пшеницы
Предусмотрено отделение оболочки пшеницы в количестве примерно 20% к массе перерабатываемой пшеницы влажностью 14%.
Преимущества:
— сокращение на 55% потребления комплексом топливно-энергетических ресурсов за счёт использования отделяемой оболочки пшеницы в качестве твёрдого топлива (низшая теплота сгорания — ориентировочно 3600 ккал/кг);
— возможность получения более транспортабельного «замеса» (смесь измельчённой пшеницы с водой);
— сокращение энергетических затрат на транспортировку продуктов на участке первичной переработки пшеницы в результате вывода из системы компонентов сырья, не участвующих в получении этанола.
Недостатки:
— незначительные потери крахмала с отделяемой оболочкой (не более 1% от исходного количества крахмала пшеницы).
- Мелкодисперсный размол пшеницы
Одним из основных факторов качественного разделения компонентов пшеницы является качество (тонина) её размола — размер частиц муки перед приготовлением «замеса» не должен превышать 250 мкм. Для реализации этой задачи в Европе, как правило, используют ультрароторные мельницы, которые отличаются большой стоимостью основного и периферийного оборудования, а также существенными эксплуатационными затратами. Для реализации аналогичной задачи компания «Техинсервис» предлагает использовать трёхстадийное измельчение пшеницы на базе вальцевых дробилок и рассевов с циркуляций полупродуктов (повторное измельчение крупного помола).
- Выделение глютена
Предусмотрено выделение из «замеса» пшеничного глютена с его последующей отмывкой от крахмала, сушкой и упаковкой. Данный продукт с массовым содержанием растительного белка не менее 70% широко используется в хлебобулочных изделиях, макаронной продукции и также востребован в мясоперерабатывающей промышленности.
Преимущества:
— возможность получения дополнительного товарного продукта, что существенно снижает срок окупаемости проекта и его инвестиционную привлекательность;
— возможность получения более транспортабельного «замеса» в виде крахмального молока с увеличением содержания сухих веществ в нём до 30% и доброкачественностью по крахмалу на уровне 87%;
— сокращение энергетических затрат на транспортировку продуктов на участке первичной переработки пшеницы в результате вывода из системы компонентов сырья, не участвующих в получении этанола.
Недостатки:
— существенная энергоёмкость процесса (ориентировочно 360 кВт электрической и 2000 кВт тепловой энергии на 1 тонну товарного глютена).
- Вакуумная ферментация
Отделение оболочки из пшеницы и выделение глютена из замеса позволяет получить транспортабельное сусло (крахмальное молоко) с содержанием сухих веществ в нём до 30%. Сбраживание сусла со столь высоким содержанием сухих веществ реализовывается посредством технологии вакуумной ферментации, что позволяет получать спиртовую бражку с содержанием этанола до 19% объемных. Существующие технологии вакуумной ферментации требуют создания ферментативных аппаратов, работающих под вакуумом, что увеличивает их металлоемкость и, как следствие, стоимость. Также существующие технологии вакуумной ферментации требуют энергоёмких компрессорных установок для перекачки всего объема углекислого газа, получаемого при брожении.
Компания «Техинсервис» предлагает альтернативный подход к реализации процесса вакуумной ферментации. Суть ноу-хау «Техинсервис» заключается в том, что процесс охлаждения ферментативного объёма (поддержание оптимального температурного режима в условиях выделения избыточного тепла) организован за счёт вскипания ферментативной массы (бражки), циркулирующей через вакуумную камеру, и перегретой относительно температуры линии насыщения вакуумной камеры, находящейся под разрежением -0,95 бар (избыточных).
Преимущества:
— возможность получения спиртовой бражки с усреднённым объёмным содержанием этанола до 19% и как следствие — уменьшение на 25% затрат тепловой энергии при переработке спиртовой бражки в браго-ректификационном отделении;
— возможность организации процесса ферментации в диапазоне оптимальных содержаний этанола в ферментативной массы на уровне 9% объёмных (отсутствие ингибирующего эффекта алкоголя на жизнедеятельность спиртовых дрожжей);
— возможность получения конденсата паров вскипания ферментативной массы с объёмным содержанием этанола до 40%, что позволяет уменьшить затраты тепловой и электрической энергии при его переработке в браго-ректификационном отделении.
Недостатки:
— дополнительные расходы на электроэнергию в сравнение с классическим процессом ферментации (ориентировочно 0,1 кВт на 1 литр абсолютного этанола).
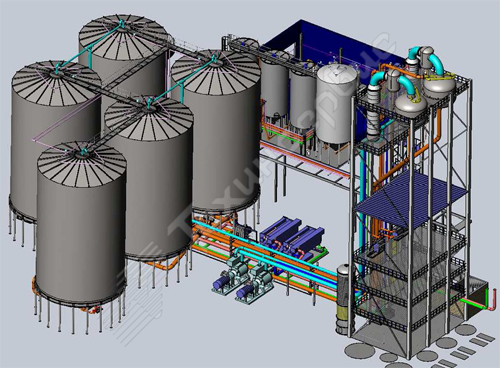
Энергосберегающая дистилляция, ректификация и обезвоживание
Принципиальная схема обвязки ректификационной колонны, обогревающей бражную колонну, представлена на рис. 3.
Также стоит отметить, что БРУ «Техинсервис» может использовать технологический пар относительно низкого потенциала (до 2,5 бар (избыточных)), что позволяет организовать обогрев БРУ вторичными парами выпарной станции сгущения спиртовой барды, работающей под давлением. Данный прием использован компанией «Техинсервис» в проекте производства пищевого спирта сорта «Люкс» для одного из спиртовых заводов Республики Болгарии.
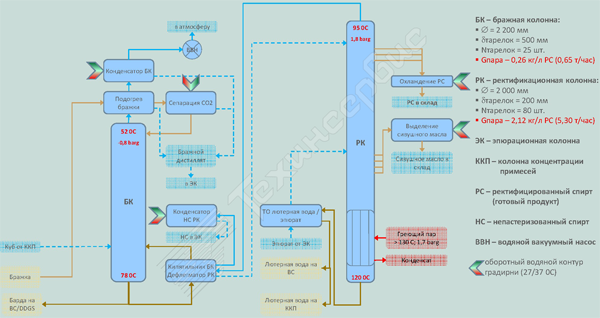
Колонное оборудование БРУ, производимое на машиностроительной базе компании «Техинсервис», оснащается высокоэффективными контактными устройствами – усовершенствованными клапанными тарелками (УКТ). УКТ имеет широкий диапазон надёжного и эффективного применения в колоннах:
— с диаметром от 800 мм до 10200 мм;
— с количеством тарелок от 1 шт. до 200 шт.;
— с расстоянием между тарелками от 100 мм до 1100 мм;
— работающих как под разряжением, так и под давлением.
— конструкцией УКТ предусмотрен механизм движения потока в клапанах, исключающий застой жидкости и обеспечивающий равномерное движение жидкости, а также увеличивает плотность пузырьков по всей площади барботажа (рис. 4);
— исключено образование осадка на поверхности УКТ, что приводит к увеличению её срока эксплуатации;
— исключено «мёртвое» пространство (застойные зоны) в местах крепления панелей тарелки в результате применения активных соединений УКТ, что приводит к увеличению производительности и КПД тарелки (рис. 5);
— применение активного соединения УКТ сокращает срок монтажа тарелки на 30-50 %;
— конструкция УКТ позволяет добиться плавного регулирования работы колонного оборудования в широком диапазоне производительности.
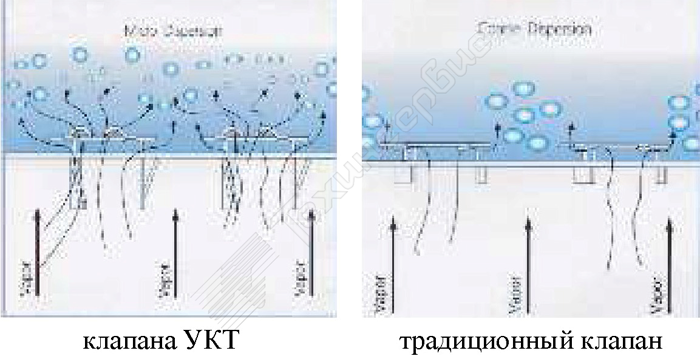
Рис. 5. Барботаж активного соединения УКТ и болтового соединения традиционной тарелки
Обезвоживание этанола
Участок обезвоживания этанола является неотъемлемой составляющей технологического процесса производства топливного этанола и производства высокооктановых компонентов на основе этанола (этил-трет-бутиловый эфир). Также при использовании этилового спирта в качестве сырья для получения химических продуктов его обезвоживание является необходимым этапом технологического процесса.
Самыми распространёнными промышленными способами обезвоживания этанола являются:
— азеотропная ректификация;
— адсорбция на молекулярных ситах;
— мембранное обезвоживание.
Последние два из перечисленных способов являются наиболее прогрессивными и экономичными, работа которых основана на использовании цеолитов.
Цеолиты (от греч. ceo lit – кипящие камни) – алюмосиликаты, которые в своем составе имеют оксиды щелочных и щелочноземельных металлов, отличаются четкой регулярной структурой пор, которые в природных температурных условиях заполнены молекулами воды. Если из пор цеолитов удалить воду, то их можно снова заполнять водой или другой жидкостью. Обратимость процесса гидратации и дегидратации цеолитов и обусловливает их использование в процессах высушивания, очищения и разделения жидкостей. Цеолиты вбирают вещества в свои адсорбционные поры. Но не все вещества могут проникнуть и остаться там. Это объясняется тем, что адсорбционные поры связаны между собой порами определенного размера. Проникнуть через поры могут только те молекулы, критический диаметр которых меньше диаметра поры.
Промышленное применение наилучшим образом нашли синтетические цеолиты марки NaA, адсорбирующие большинство промышленных газов, критический размер молекул которых не превышает 0,4 нм (в том числе и водяной пар).
Адсорбция на молекулярных ситах
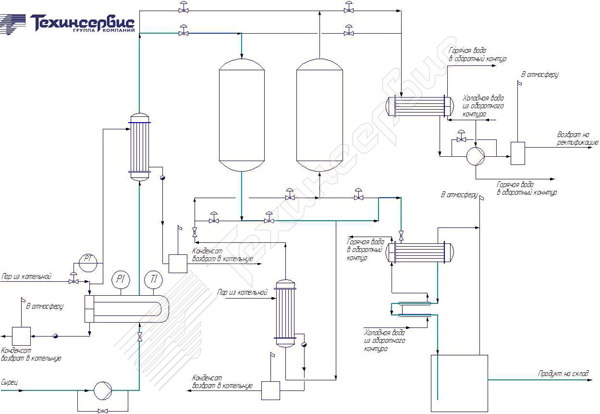
На обезвоживание поступает водно-спиртовой пар из ректификационной колонны. При повышенном давление пар проходит через один из адсорберов. Молекулы воды, которые содержатся в паре, задерживаются в порах молекулярных сит, а обезвоженный этанол выходит из адсорбера. Обезвоженный этанол конденсируется, охлаждается и отводится в сборник. После насыщения водой молекулярных сит в первом адсорбере, работа которого контролируется по содержанию воды в обезвоженном этаноле, подачу водно-спиртового пара переключают на второй адсорбер. При работе на втором адсорбере в первом при помощи вакуумного насоса (через конденсатор) создают вакуум. За счет изменения температур кипения среды в адсорбере при значительном изменении давления проходит испарение воды, удержанной молекулярными ситами. Для предотвращения значительного охлаждения молекулярных сит в первом адсорбере во время выпаривания воды, часть пара обезвоженного этанола после второго адсорбера перегревается и возвращается в первый адсорбер. Водно-спиртовой пар, который выходит из первого адсорбера, конденсируется, отводится в сборник и возвращается на переработку в ректификационную колону. За время работы второго адсорбера проходит регенерация молекулярных сит в первом адсорбере. После чего подача водно-спиртового пара из ректификационной колоны снова переключается на первый адсорбер, а второй – переводится в режим регенерации под вакуумом, и цикл повторяется.
Описанный выше процесс, на сегодняшний день, является самым распространённым способом обезвоживания этанола в мире. В 2002 году компанией «Техинсервис» была реализована данная технология на одном из спиртовых заводов Чехии (работает и сегодня). В то же время на сегодняшний день технология считается устаревший, а периодичность работы, наличие регенерации и высокий уровень эксплуатационных и энергетических затрат привели к развитию и внедрению компанией «Техинсервис» других, более прогрессивных, методов обезвоживания.
Мембранное обезвоживание
Мембрана цеолита NaA используется для обезвоживания различных сред, в том числе и этанола. В случае протекания процесса в жидкой фазе процесс называется «первапорация», в случае с паровой фазой – «паровая проницаемость».
Цеолитовые мембраны используются в виде тонкого слоя, нанесённого на керамическую основу, что позволяет вести процесс с большими потоками. В промышленных масштабах предпочтительнее использовать нанесение цеолитового слоя на внутренние поверхности керамических элементов (трубок) во избежание механических повреждений и организации оптимального потока. Цеолиты типа NaA в виде мембран могут наноситься на трубчатые основания, представленные моноканальными либо многоканальными трубами.
Использование цеолитовых мембран позволяет вести процесс обезвоживания при более высоких параметрах (давление – 5,5 бар (избыточных) и температура – 135˚С), что выгодно сказывается на металлоёмкости инсталляций.
Оборудование по обезвоживанию, основанное на работе цеолитовых мембран, благодаря своей высокой селективности, надёжности и долговечности, превосходит существующие аналоги: молекулярные сита и полимерные мембраны.
Стоит отметить, что компания «Техинсервис» на собственной машиностроительной базе серийно производит весь спектр специфического технологического оборудования, входящего в комплексы обезвоживания этанола, работающие как по технологии мембранного обезвоживания, так и по технологии обезвоживания на молекулярных ситах или азеотропной ректификации.
Принципиальная схема процесса обезвоживания этанола по технологии мембранного обезвоживания компании «Техинсервис» представлена на рис. 7.
Рис. 7. Принципиальная схема обезвоживания этанола компании «Техинсервис»
по технологии мембранного обезвоживания
На обезвоживание поступает водно-спиртовой пар из ректификационной колонны, который поступает в межтрубное пространство мембранного модуля. Водяной пар, величина молекул которого меньше пор селективной мембраны, проходит сквозь керамическую трубку с цеолитовым напылением и увлекается вакуумным насосом. Пары этанола, величина молекул которого больше пор селективной мембраны, выходят из аппарата и поступают на конденсатор обезвоженного этанола. Движущей силой проникновения водяного пара сквозь цеолитовую мембрану является разность давления между трубным (создается вакуумным насосом) и межтрубным пространством (создается греющим паром выпарного аппарата и конденсатором обезвоженного этанола).
Описанный выше процесс не требует регенерации и характеризируется высоким КПД и, как следствие, отличается самыми низкими эксплуатационными и энергетическими затратами. В рамках государственной программы реконструкции спиртовой отрасли Украины, в 2008 году компания «Техинсервис» внедрила данный процесс на пяти спиртовых заводах Украины. Общая производительность проекта – 125 тыс. тонн топливного этанола в год.